Common turbo failure – REA/ SREA/ UTA Smart/ UTA Simple
REA/ SREA/ UTA Smart/ UTA Simple Failure Modes
REA (Rotary Electronic Actuator), SREA (Simple Rotary Electronic Actuator) or UTA (Universal Turbo Actuator) are fitted to a variety of different variable geometry turbos and control the variable vane movement. This article explores the causes and the signs of REA/ SREA/ UTA Smart/ UTA Simple failure to help you identify this failure mode when repairing.
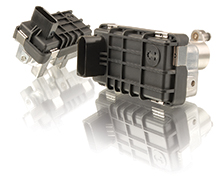
Why do REA/ SREA/ UTA Smart/ UTA Simple electronic actuators fail?
REA/ SREA/ UTA Smart/ UTA Simple electronic actuators are highly complex and intricate. They are not interchangeable with different gearboxes or black caps. The calibration settings are programmed in the software within the black cap and are unique to each turbocharger. The majority of REA/ SREA/ UTA Smart/ UTA Simple failures are identified by the engine management systems. However, the electronic actuator may not be the primary cause of turbocharger failure, it is likely to be another underlying reason that caused the failure.
Causes of REA/ SREA/ UTA Smart/ UTA Simple electronic actuator failure:
- Gearbox Failure – REA/ SREA/ UTA Smart/ UTA Simples will fail if the nozzle ring assembly has any form of restriction, this could be due to sludging or carbon build-up. When the nozzle ring assembly is restricted, it pulls a higher current through the motor than it is designed to take, this therefore causes the motor to burn out or the plastic worm gears to fail. This restriction can reduce boost pressure and can result in the vehicle being put into ‘limp home mode’. In most failures, the black cap and electronics are unaffected by the gearbox failure and can be reused.
- VNT System Fails/Seizes – Caused by sludge or carbon build up around the VNT blade system.
- Damage to the Board Connectors – The connectors can break through expansion and contraction with heat. Connectors can also appear to be working fine when cold but once the engine warms up a fault can appear.
- Mishandling of the Turbo – If the turbo connector is knocked or banged, it will break and the whole unit will need replacing.
- Water Ingress – The location of a turbo in the engine compartment can mean the electronic actuator is more susceptible to water ingress. The actuator can become rusty and contaminated, giving the wrong signals and ultimately breaking.
- Engine Vibration – Constant vibration from the vehicle could wear out components within the electronic actuator, causing it to fail over a period of time.
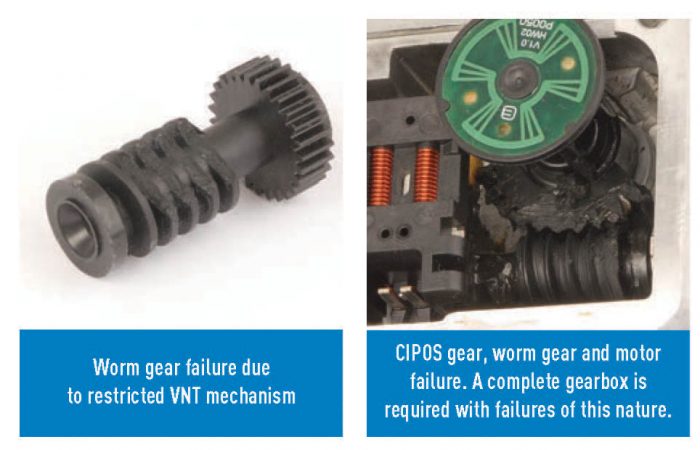
Signs of REA/ SREA/ UTA Smart/ UTA Simple electronic actuator failure:
- Engine management light or other warning lights
- A complete loss of power, causing the vehicle to go into limp-home mode
- Low boost
- Over boost
- Noise from the turbocharger
- Fault codes
Preventing turbo failure caused by REA/ SREA/ UTA Smart/ UTA Simple electronic actuator failure
- When repairing electronic actuators, you need to change all the damaged/effected components
- Check all connecting wires
- Ensure bolts are tightened to the correct torque setting
- Check the VNT mechanism for restrictions
- Check the wiring harness condition
- Check black cap is free from damage
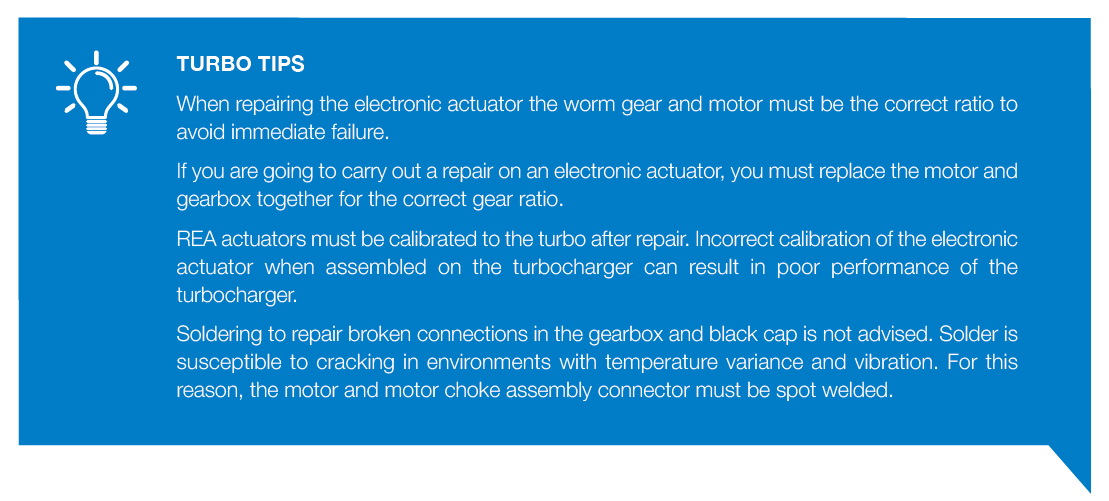
For further information on this or other topics, please contact Melett Technical Support – [email protected].